How extrusion works
Extruding is a continuous process that takes place 24/7 at KIVO. This involves heating and melting PE pellets in a cylinder with a rotating screw, the extruder. This screw forces the molten material forward and through an extrusion slit, giving it the desired shape. From the nozzle comes a thin-walled tube that is inflated with air to form a huge plastic balloon. After cooling, the film wrapped and possibly cut open, ready for further processing.
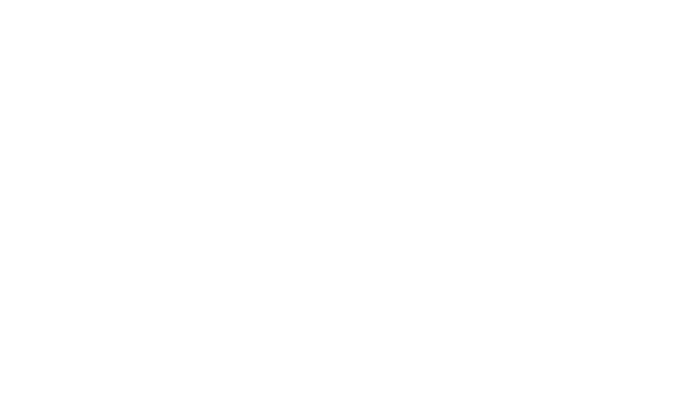
Durable extrusion
Within the extrusion department, sustainability plays a crucial role. We lead the way in thickness reduction and have minimal production waste, which we recycle ourselves at KIVO Recycling. We develop optimal films with a high percentage of recycled content from our own recycling plant REKS. Our insulated extruders are cooled with a closed circuit of bottom-cooled spring water. We were awarded the first prize for the MYA efficiency plan, due to our energy-efficient production processes.
Want to know more about our sustainable initiatives?
Our various extruders
KIVO's machinery has grown and developed considerably since its establishment in 1966. The current machinery has 40 extruders, including 30 mono-extruders and 10 co-extruders. By using the latest technologies, training and good relations with machine suppliers, we remain at the forefront of innovative products.
Thanks to coextruders, KIVO can films produce with multiple layers, tailored to your specific requirements and needs. This offers possibilities such as different colours inside and outside (e.g. potting soil bags), good sealability on the inside and a smooth surface on the outside, and barrier-enhancing additives in the middle layer.
With customers in dozens of industries across more than 30 countries, we extensively select and test specific formulations. Various additives can be used to give special mechanical or aesthetic properties, such as friction resistance, tensile strength, static, puncture resistance, adhesion, sealability, flame retardancy, UV resistance, colouration and odour neutralisation.
Frequently asked questions
Below are some frequently asked questions about extrusion.
What is extrusion and how does KIVO use this technique?
Extruding is a process in which plastic granules are heated and pressed through a mould to (tube)films and other products. At KIVO, we use advanced extrusion machines to produce high-quality and durable packaging films that are tailor-made for different applications.
What types of packaging solutions does KIVO produce with the extrusion process?
KIVO produces several varieties films, including mono and multilayer films, which are suitable for a wide range of applications such as food packaging, industrial packaging and more. Our product range includes: Bread bags, Bag loaders, Bag inserters, Recy-wrap film, Paperlike
Papermatch, tubular film, shrink film, crate bags, freezer film, barrier film, FFS film, Butter film, Spice packaging, meat sheets and bags, fish sheets and bags, Fruit bags, Vegetable bags, Cucumber film, Pet food packaging, Liner film, Covering film, sleeves and sheets, Anti-slip sheets, Container sleeves, Pallet sleeves and sheets, Shipping film and bags, Cement bags, Tape film, Furniture covers, Garbage, collection and rubbish bags, Clothing and dry cleaning covers, Car spray film and car seat covers, Mailing film, Woodpellets bags, Potting soil bags, Fertiliser bags, Spreading salt bags, Gravel bags, Sand bags, Flower and rose film, Potato and chip bags, Packaging for candles.
How does the extrusion process contribute to the sustainability of KIVO's products?
Our extrusion process is designed to minimise material waste and be energy-efficient. In addition, we use recycled material in our films, reducing the carbon footprint of our products.
Can KIVO incorporate specific customer requirements into their products?
Yes, KIVO offers customised packaging solutions that meet our customers' specific requirements and needs, from thickness and strength to other specific material properties.